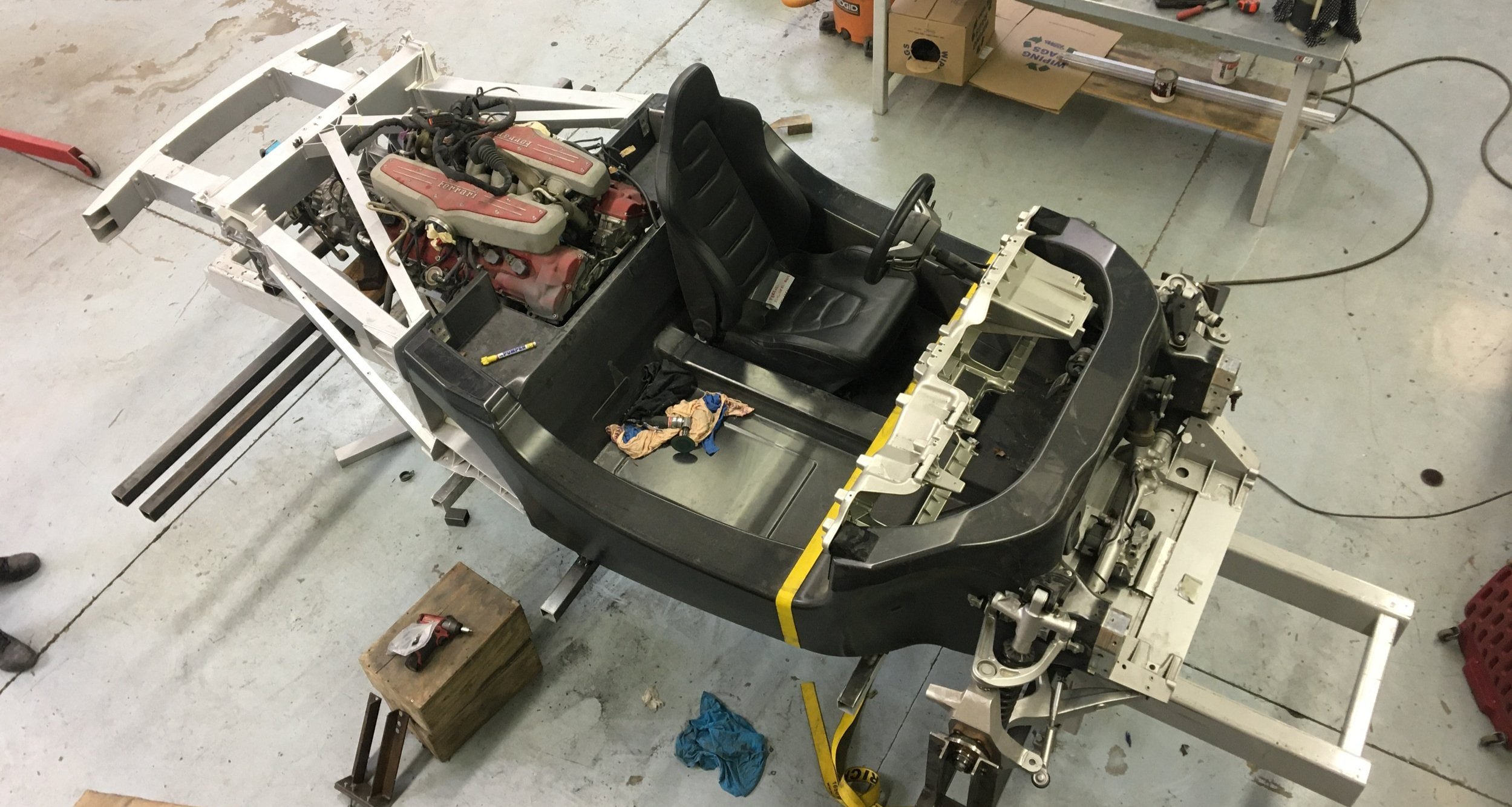
This is what happens when you spend too much time on the internet.
This is a fun one. A McLaren MP4-12C display chassis purchased off of a popular auction site married with the V12 from a 599 GTB, driving the rear wheels through a flipped 996 transaxle and riding on suspension pulled from the IndyCar parts bin.
The Ferrari V12 is just a bit longer and heavier than the Nissan-based V8 these rolled out of the showroom with, hence the extensive cutting of the tub. Some wheelbase adjustments were made to keep the weight distribution reasonable as well. When you have a carbon tub with fixed suspension attachment points, axles in different locations than intended, lower ride height, and radically wider tires, how do you go about packaging the front suspension and keeping the geometry in check?
The first thing you do is make drawings on the computer. A lot of drawings. This project was tackled before I had 3D scanning readily at my disposal, so painstaking measurements of the tub and all suspension points were taken. They were checked and re-checked. The tub and all relevant points were modelled. From here, the wheels, tires, and all other critical parts can be modelled and placed in alignment as intended. KPI and other suspension geometry are sketched, workpoints are made, and the entire problem becomes a big game of connect-the-dots.
The rocker links are laser cut 4130 and utilize a precision turned center bearing carrier. Geometry is chosen to achieve the desired amount of progressive wheel rate in compression. Pushrod and shock alignment are refined to minimize thrust/axial loads as much as possible, but IGUS bushings are utilized to deal with those loads. Bushings offer lighter weight, more compact solution than bearings in this application.
Being constrained by the existing suspension attachment points while moving the front axle back leads to some fun problem solving with the control arms. 4130 aero tubing is utilized for improved rigidity in critical directions, and formed gussets were made reinforce critical areas.
With the DPi-sourced tires being many inches wider than the original rubber but the overall width of the vehicle still similar, real estate between the tire and the tub is at a premium. There’s simply no room to package a damper and reasonable upper control arm. Pushrods are a necessity.
Uprights are substantially modified from their original form. The original mounting point for the upper ball joint bracket is utilized, but the bracket is a fabricated piece to suit the new geometry. The steering arm position is carefully chosen to minimize bump steer and allow for tuning of exact bump steer behaviour.