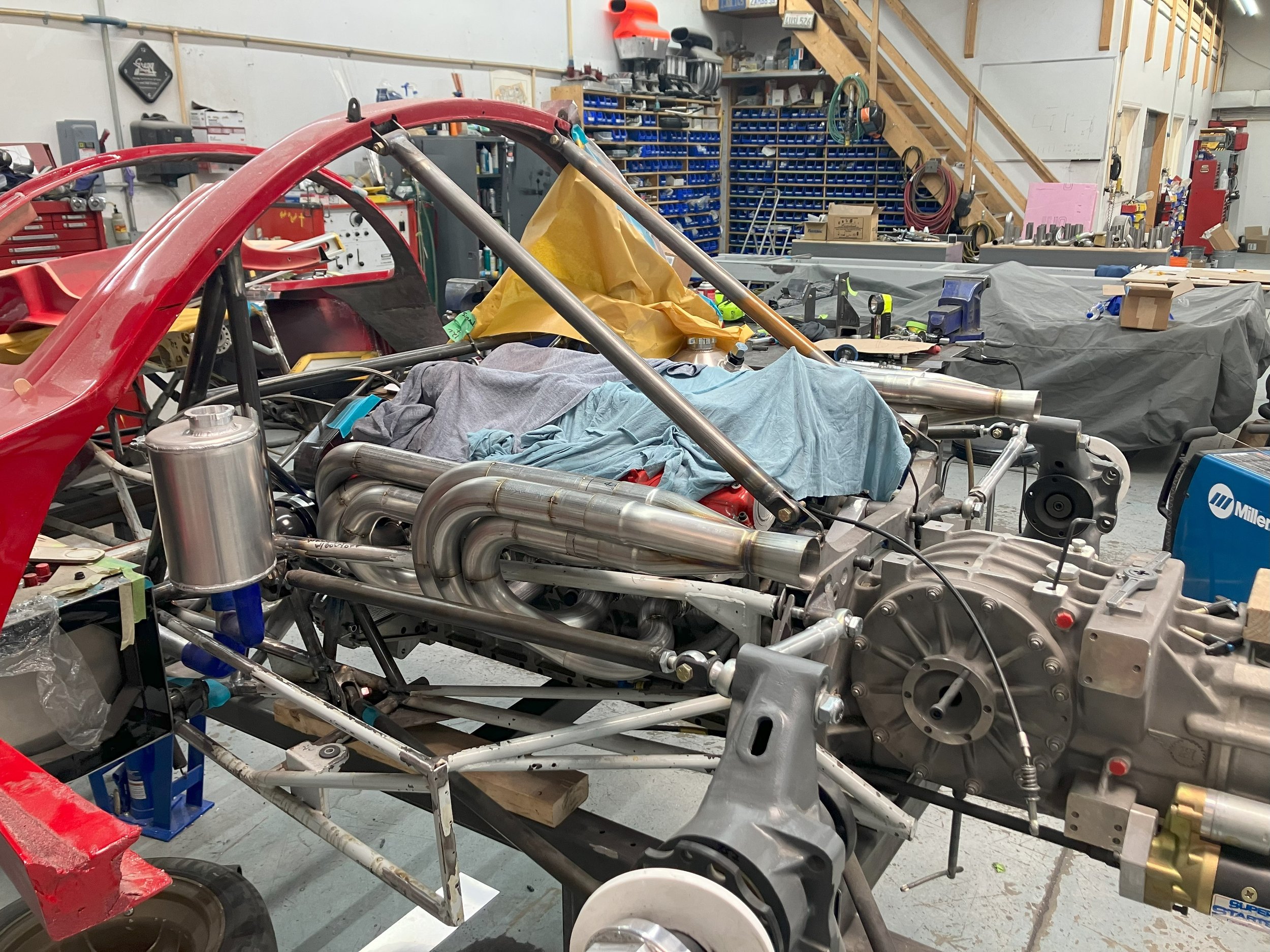
Purists be damned.
The Ferrari 330 P4. One of the most revered cars from all of history. It’s something to be observed only in fleeting glimpses at the most prestigious concours events. It’s to be appreciated like a fine painting or a vintage wine. It’s beauty and historical significance command the respect of all.
Or that’s what someone else might tell you. There’s a time and place for that, but it’s not here or now. This “reimagining” would make a Ferrari connoisseur nauseous. It features a carbon fibre body, a genuine Ferrari 512S frame that’s been modified extensively, a Hewland transaxle, and a V12 sourced from Prodrive’s 550 Maranello GT1 effort of the mid 2000s. Nothing is sacred.
This frame and drivetrain combination presents numerous complications. The engine was never intended to be mated to a transaxle, and originally located the oil filter inside the bellhousing. The oiling system was extensively modified to make use of a transaxle possible. The exhaust port locations on this engine are lower and wider than the 512’s original engine, which complicates packaging. 3 primaries had to fit inside the frame, 3 between the frame and suspension, and all collectors had to stay within the compact bodywork, so 3D scanning was utilized.
Scanning allowed for many iterative design steps in CAD before any fabrication took place. Packaging was refined to allow for as much serviceability as possible with the manifolds in place while still maintaining the desired length of each runner. The model was converted into a spreadsheet detailing the exact radius and length of each bend and straight section, simplifying the ordering process and minimizing material waste.
Fixturing was done in the standard way, with the collectors and head flanges held solidly in place on a fabricated steel fixture. Work holding utilizing 3D printing and a fixture table is possible and even my preferred method, but the lack of a fixture table prohibited that in this case.
The head flanges were CNC machined specifically for this project from 304 stainless, and feature a precise socketed fit with the 1.75” primaries. All joints were fitted and tacked without any filler to ensure proper fitment and to allow for the best possible final weld. Care was taken to ensure precise alignment of all primaries entering the collectors to achieve the best possibly slip joint seal.
To ensure each bent section was cut to the dimensions specified by the CAD model, I created a special tool to precisely mark the tubing. Read more about that tool here.
Concept to reality.

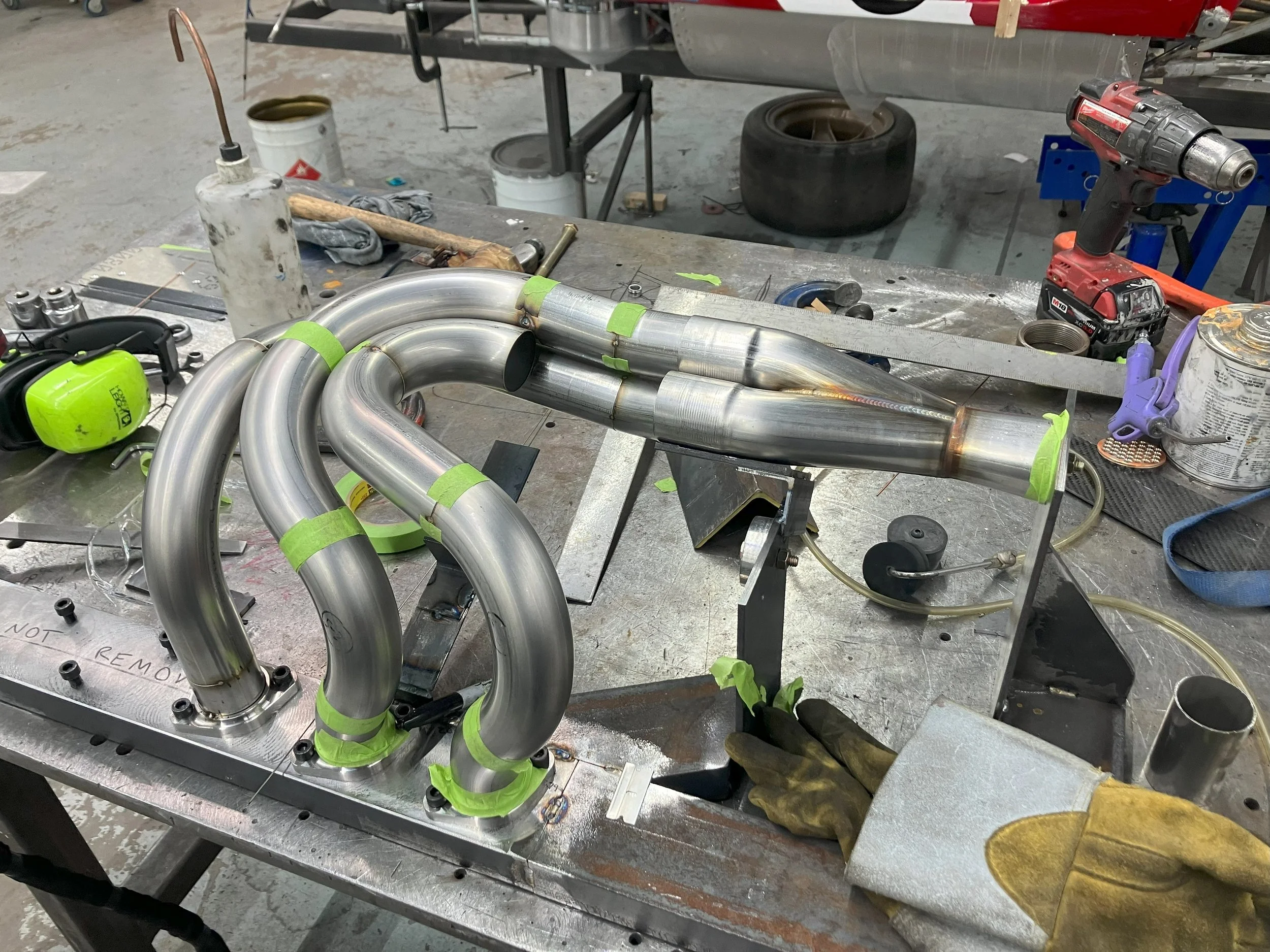
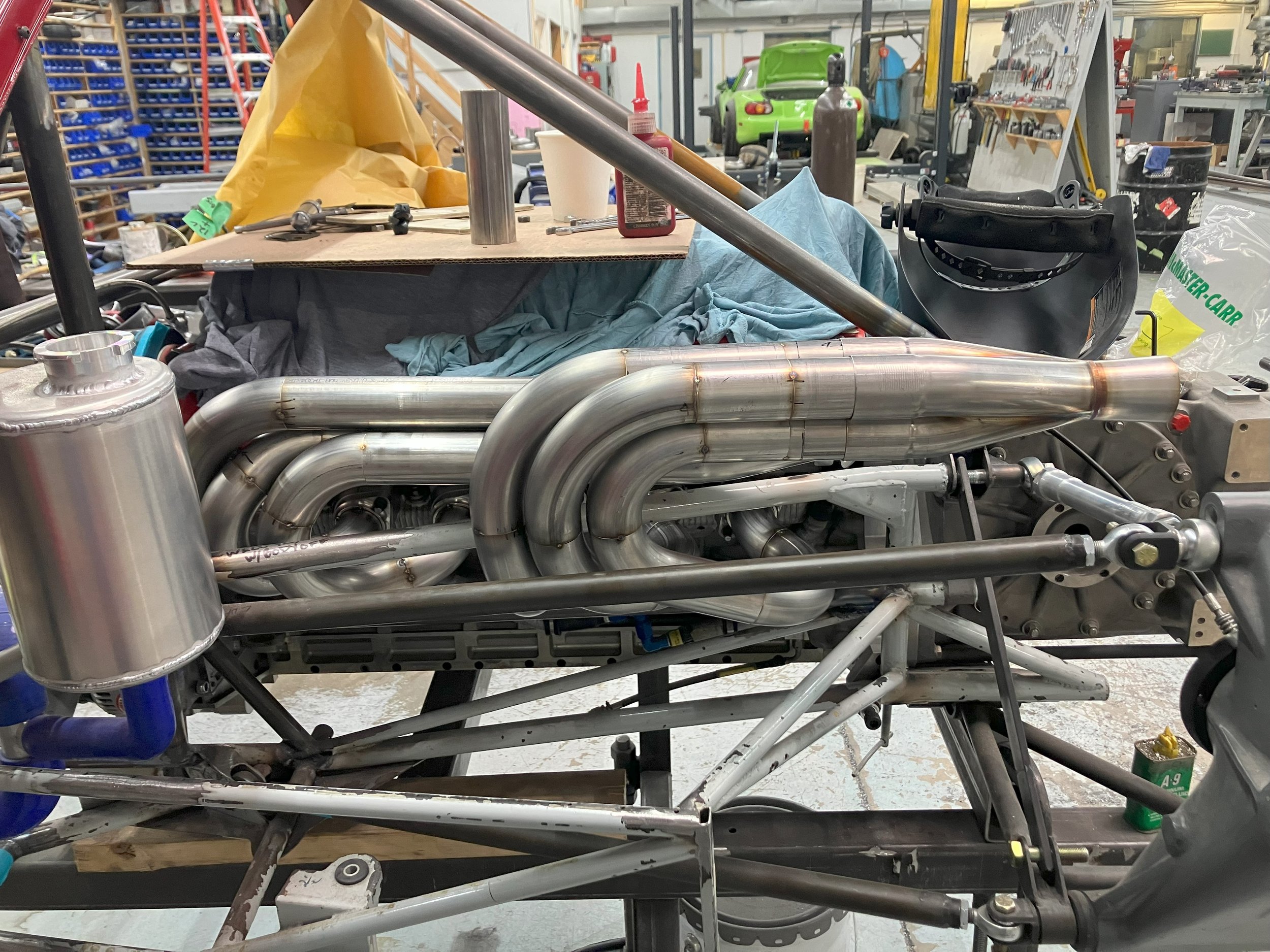


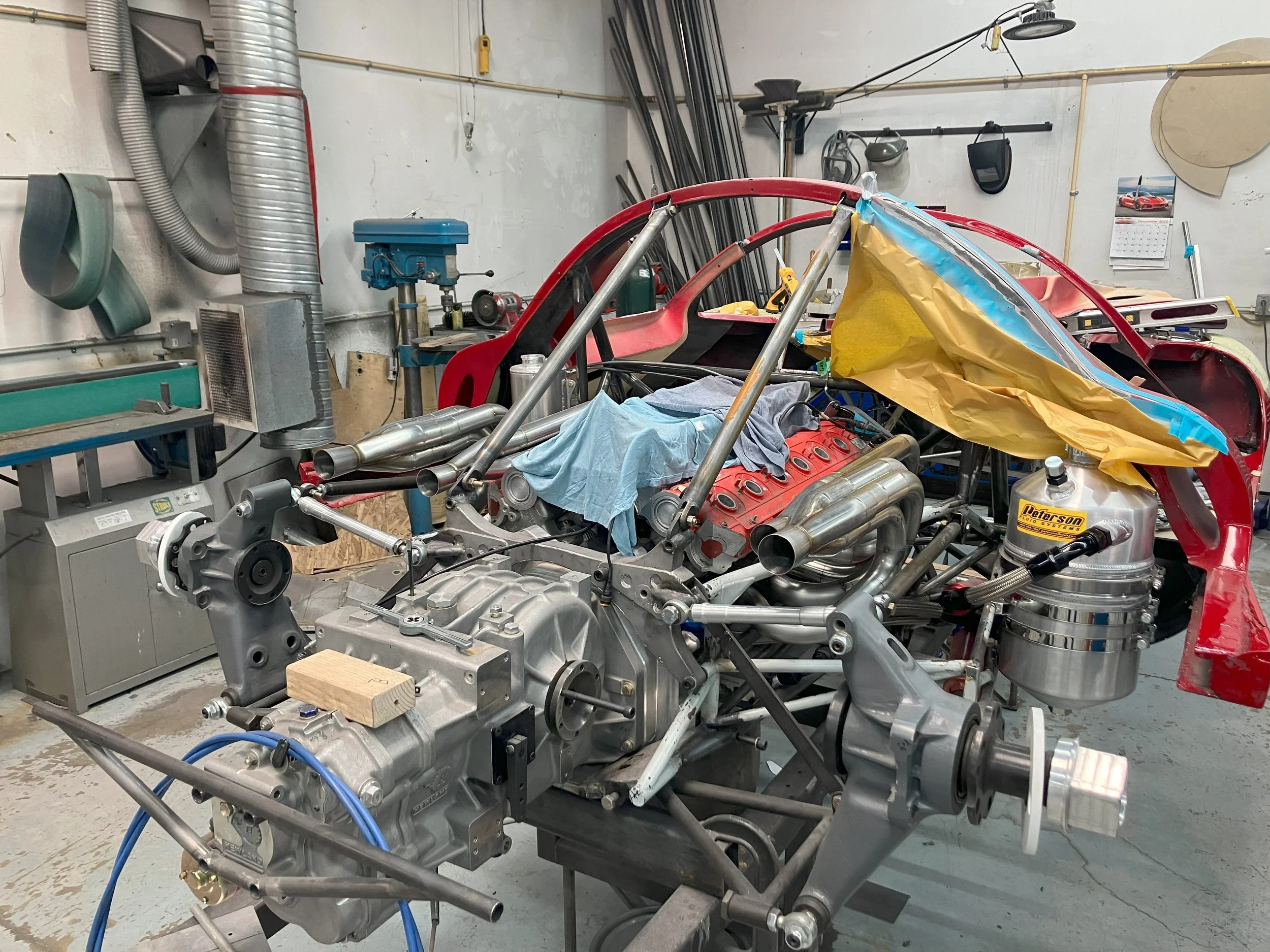
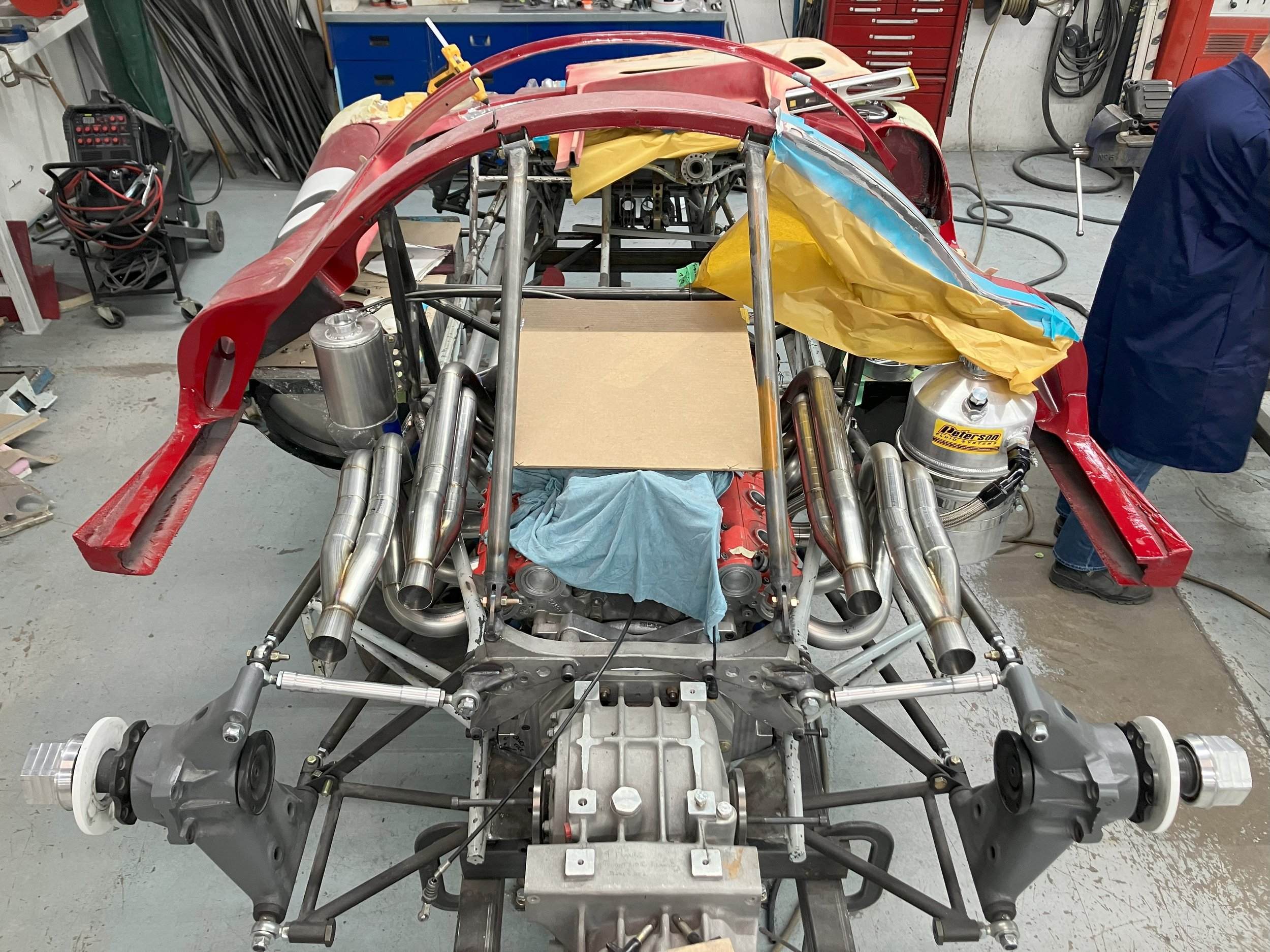